Assembly Line Development and Integration
Drive Unit and Inverter Assembly Lines
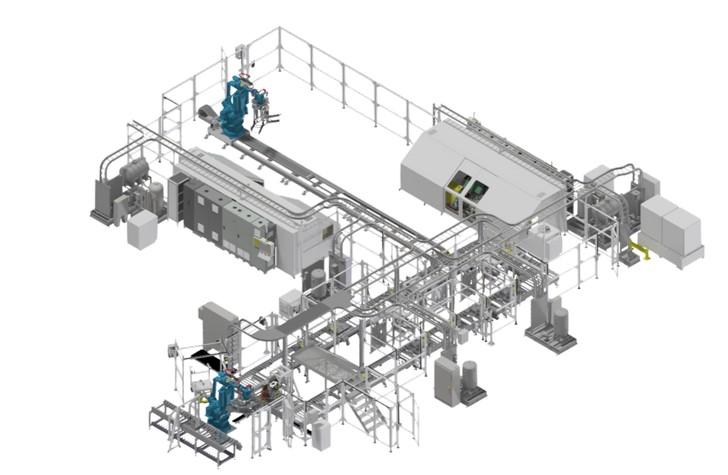
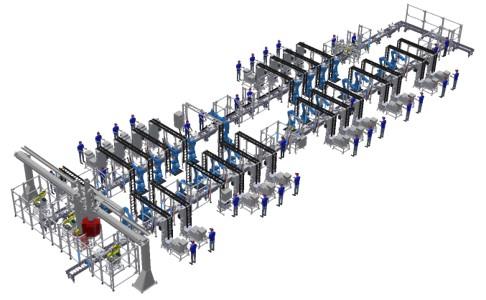
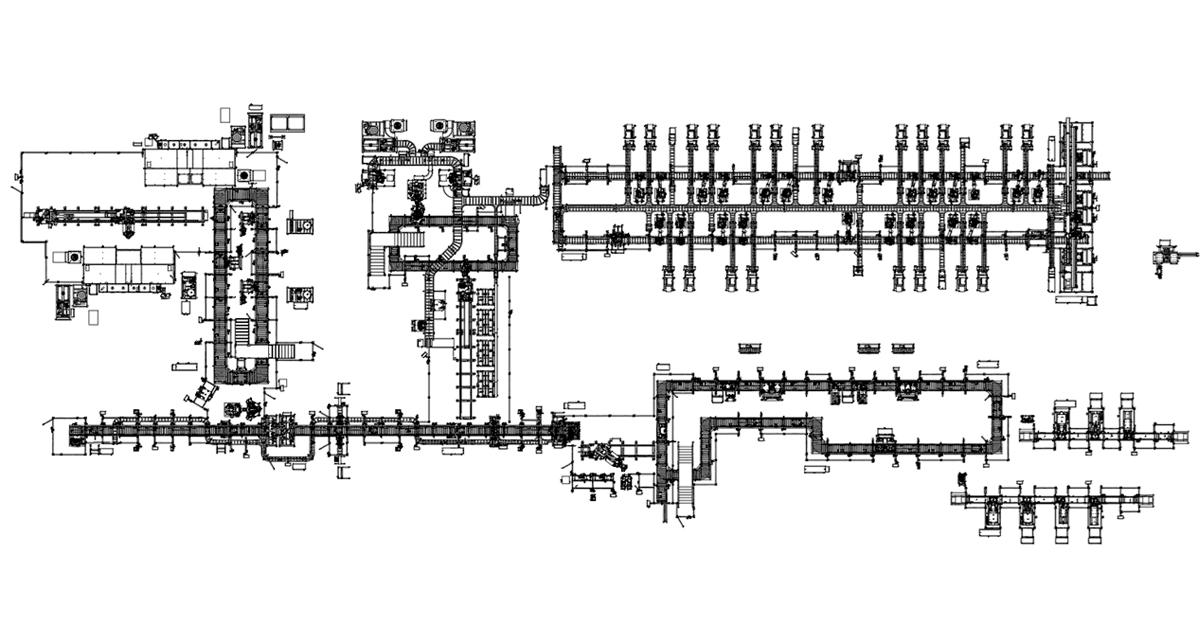
Inverter Assembly Line Features:
- (20) Fastening Robots
- (2) Robotic Inspection Stations
- (4) Robotic Soldering Stations w/ AOI Inspection
- (1) Material Handling Gantry
- (2) End of Line Testing Material Handling Robots
- (2) Rejection Spurs
- (42) Automatic and Manual Work Stations
- Each conveyor is individually motorized and contains RFID readers and lift & locate systems for pallet positioning
- Each Pallet contains RFID tags and bushings for accurate locating
- ESD rated conveyor, pallets, and process
Drive Unit Assembly Line Features:
- 115 Total Stations
- 3 Robots
- 2 Assists
- 101 Total Conveyor Stations
- Each conveyor is individually motorized and contains RFID readers
- Lift & Locate systems for pallet positioning in auto stations
- Each pallet contains RFID tags and bushings for accurate locating
- 50% of buffer stations are populated with pallets for optimal buffering
- Station Quantities:
- M01 Gear Assembly: 14 Stations & 1 Assist
- M02 Gear Assembly Line: 12 Stations & 1 Assist
- Shield Assembly: 34 Stations
- Shield Marriage: 3 Stations & 1 Robot
- Assembly Conveyor: 29 Stations
- End of Line Cell: 20 Stations & 2 Robots
Crankshaft Material Handling Gantry
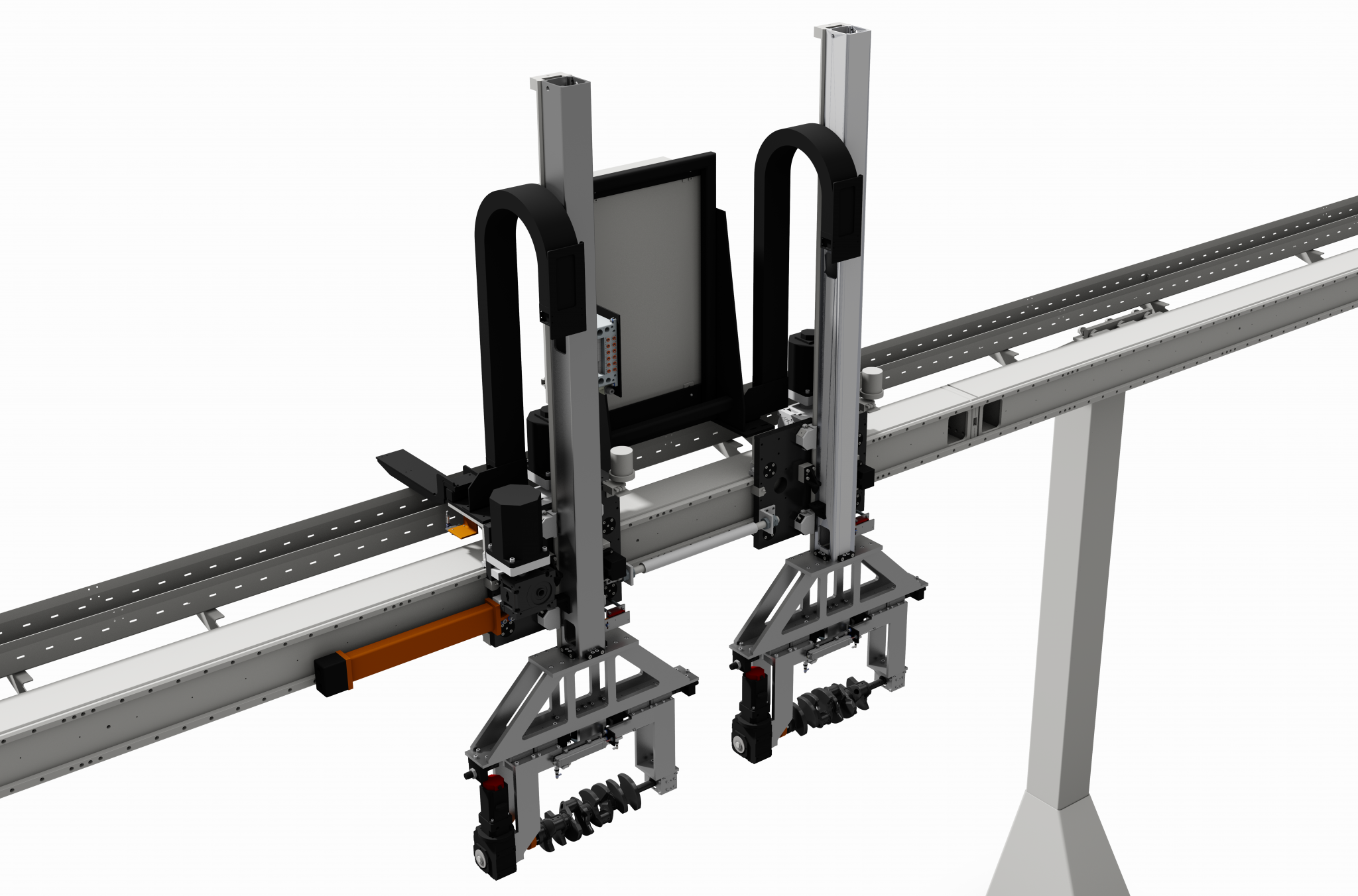
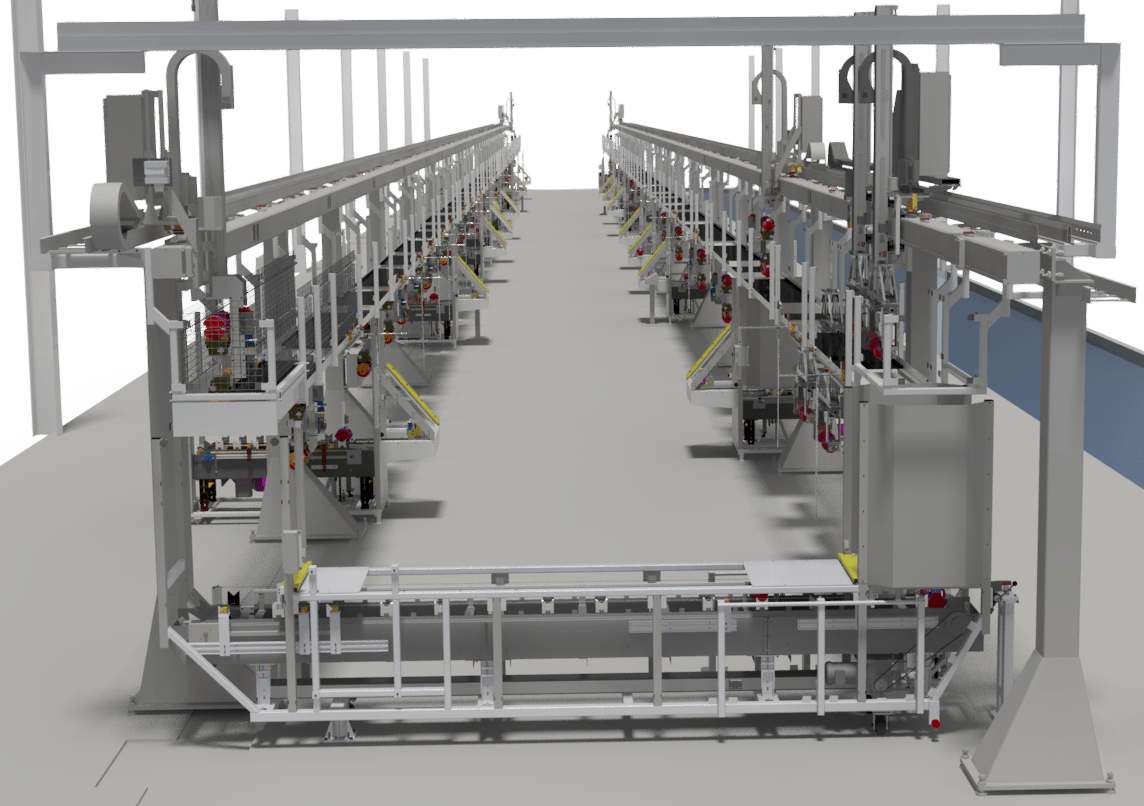
Features:
- 650 Foot Long 17 axis Servo Gantry Crankshaft Loading System
- 14-Crankshaft Loading, Buffer, Crossover and Unload Conveyors
- Multiple Quality Control Takeout Stations
- 17 Operator HMIs
- Integration of dozens of unique machines including bar code marking, data, and part tracking through grinders, lathes, balancers, hardeners, washers, gauges, mills, laser markers, conveyors, etc.
Check out this this Youtube video we did with Fanuc on our Crankshaft Machining Center Servo Gantry Loading System.

Robotic Ring Gear Deburring Line
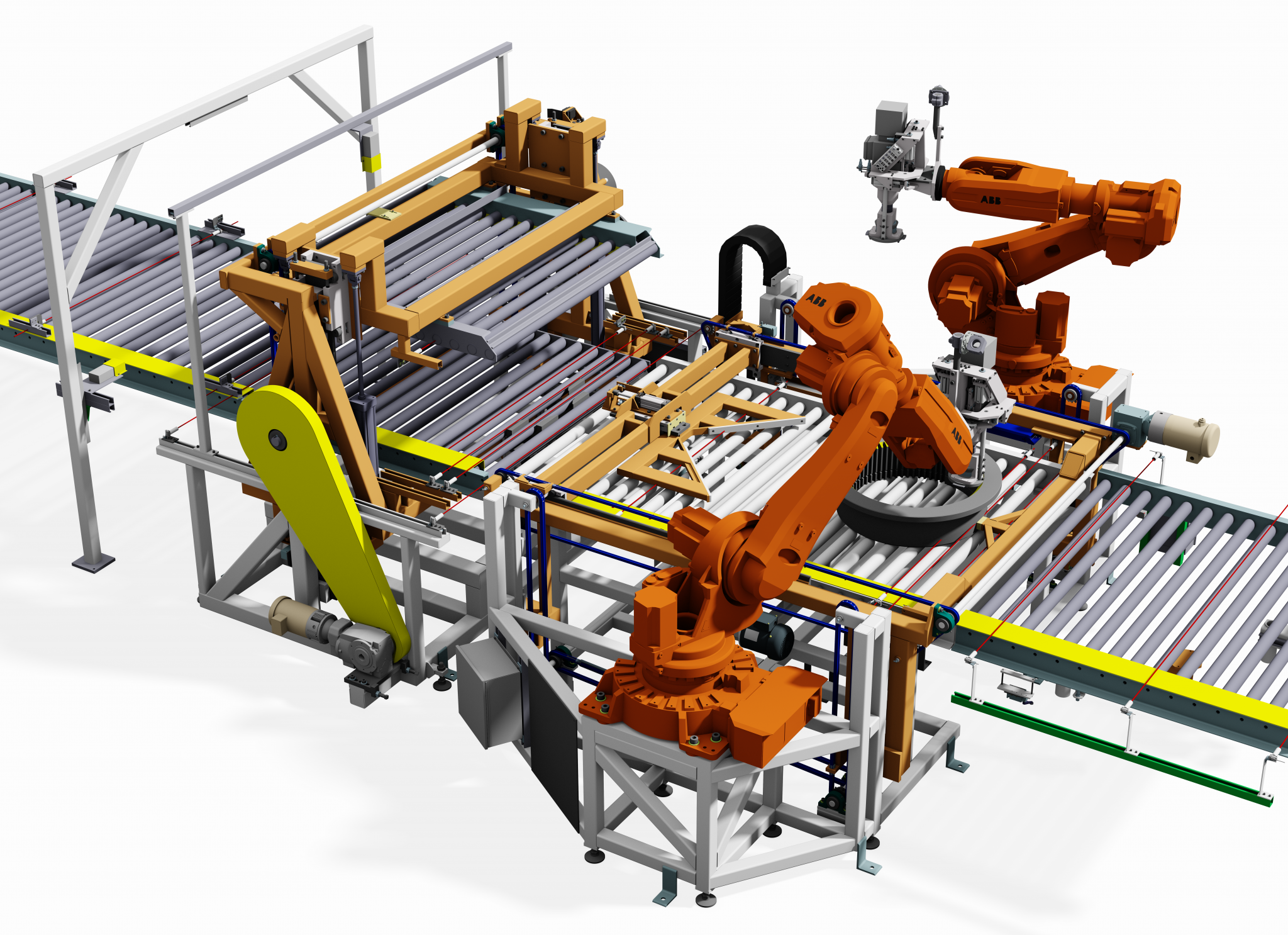
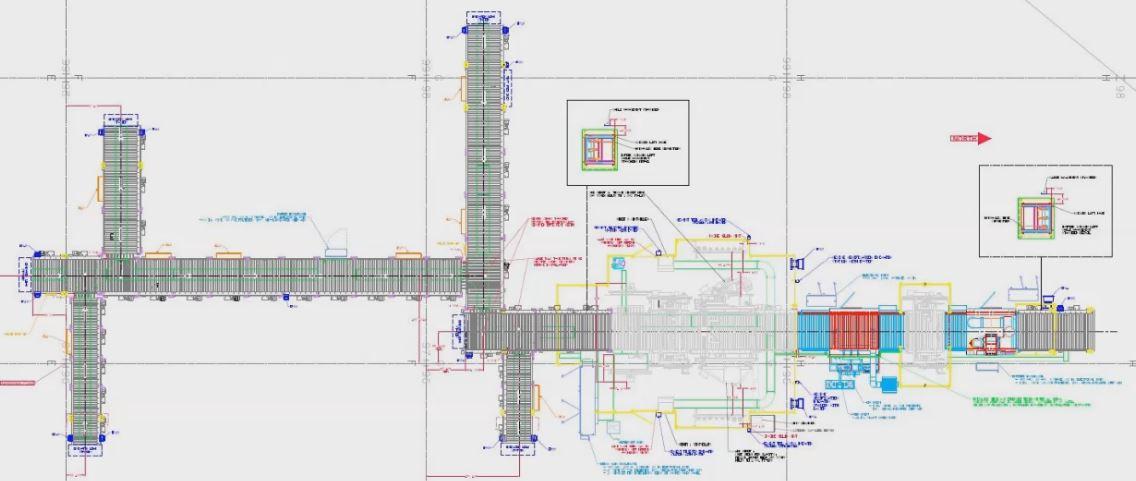
Features:
- A driven roller conveyor feed parts into the deburring cell from multiple upstream processes
- Automatic part detection identifies inbound parts and configures the system for automatic processing of the inbound part
- Inbound and outbound roll-over stations allow for deburring on both sides of the part, regardless of how it is conveyed into the cell
- Robotic deburring station utilizes two robots and automatic tool changers for on-the-fly tool changes
- Integrated washer and blow-off system for cleaning of parts after deburring process
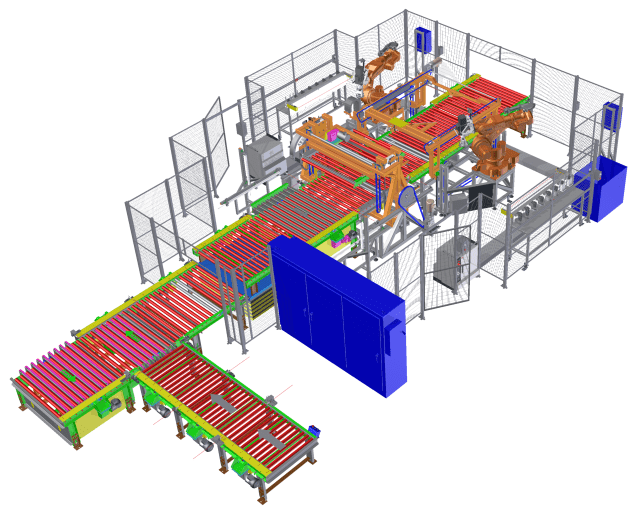
Engine Cylinder Head Assembly Line
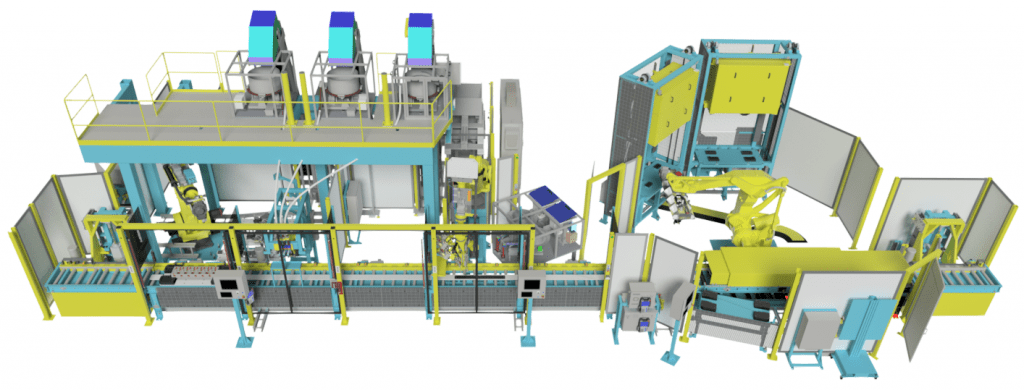
Features:
- 63 feet long recirculating pallet conveyor with elevators on each end
- Utilizes a total of five Fanuc robots
- Multiple manual and automated assembly stations
- Accommodates three different models of engine cylinder heads with the flexibility to accommodate additional future models
- Utilizes three bowl feeders for orienting and accumulating different size springs for each model
- Utilizes two bowl feeders for orienting and accumulating small keepers
- Utilizes two custom cam-designed cylinder head spring exercisers for testing and quality assurance
Vehicle Accumulation and Transfer Line
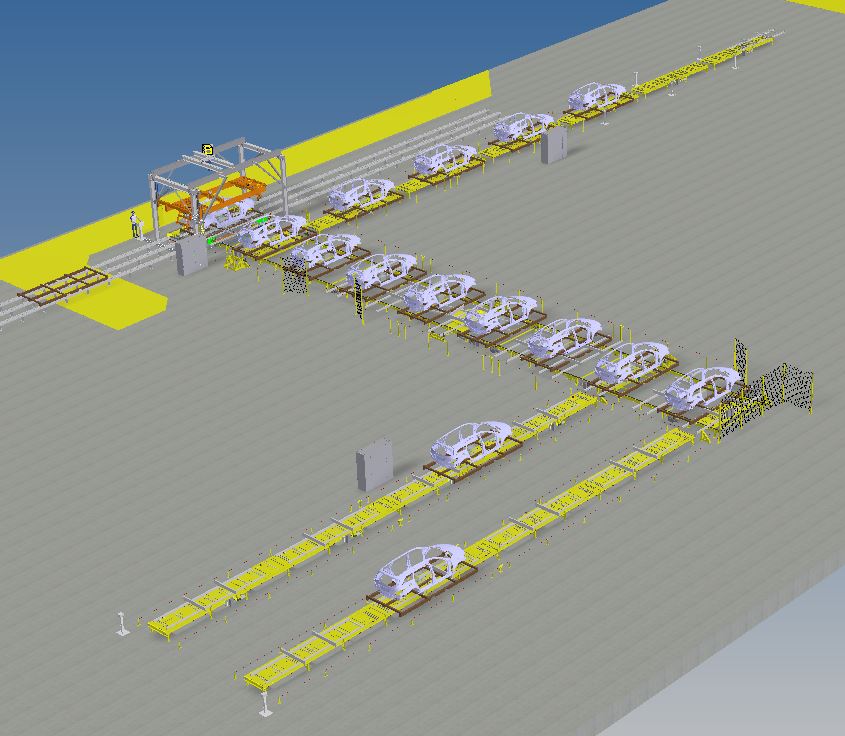
Features:
- Body Transfer System
- 470 Feet Of Driven Roller Conveyor
- Two-Strand Side Winders
- Vehicle Body Lift
- Skid Loading System
- Painted Body Load And Unload
- 2-Hydraulic Scissor Lifts
- Lift And Transfers Between Steel & Wood Skids
- Turntable To Rotate Skids 180°
Bearing Cap Assembly

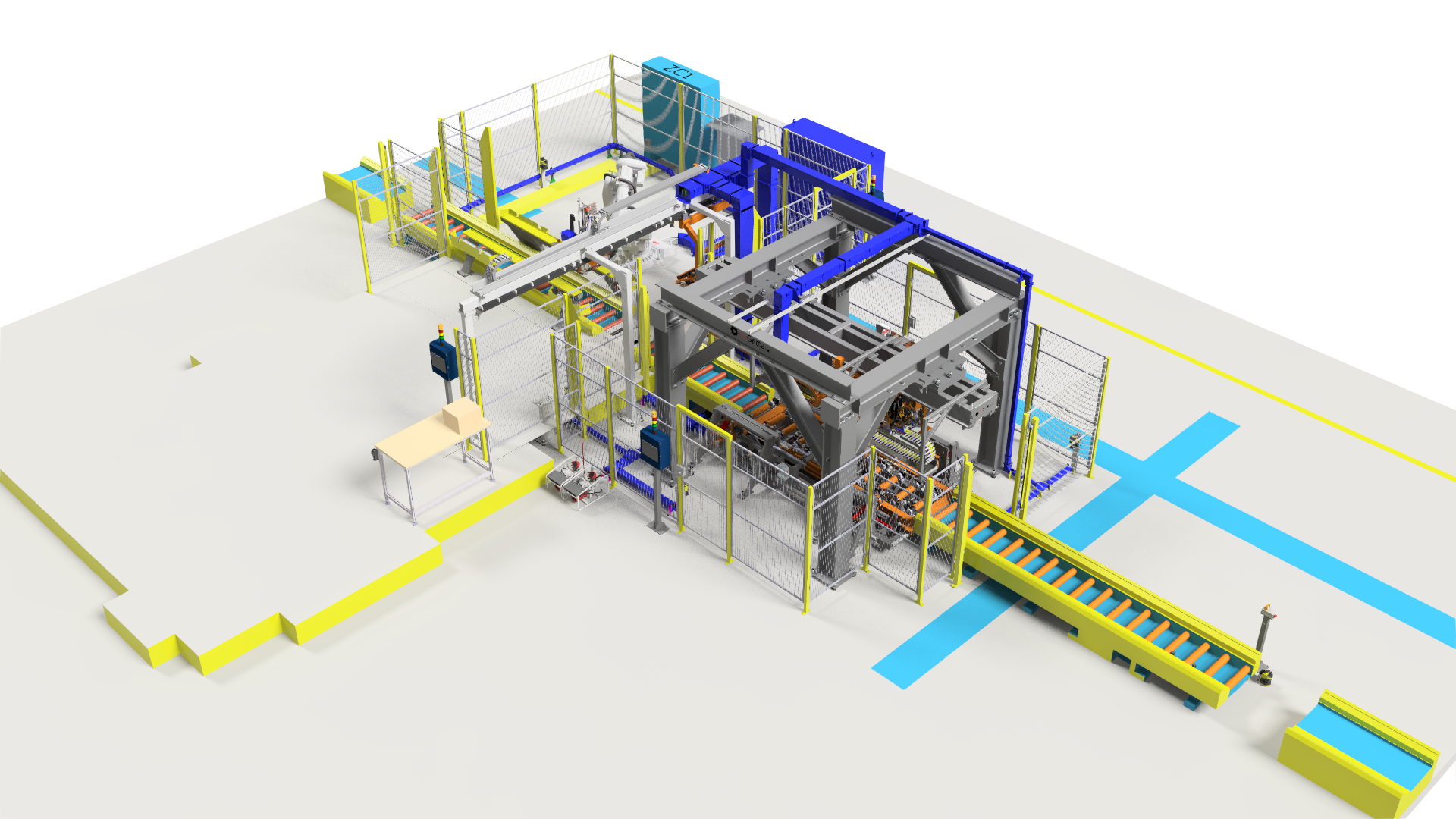
Cylinder Head Assembly Line
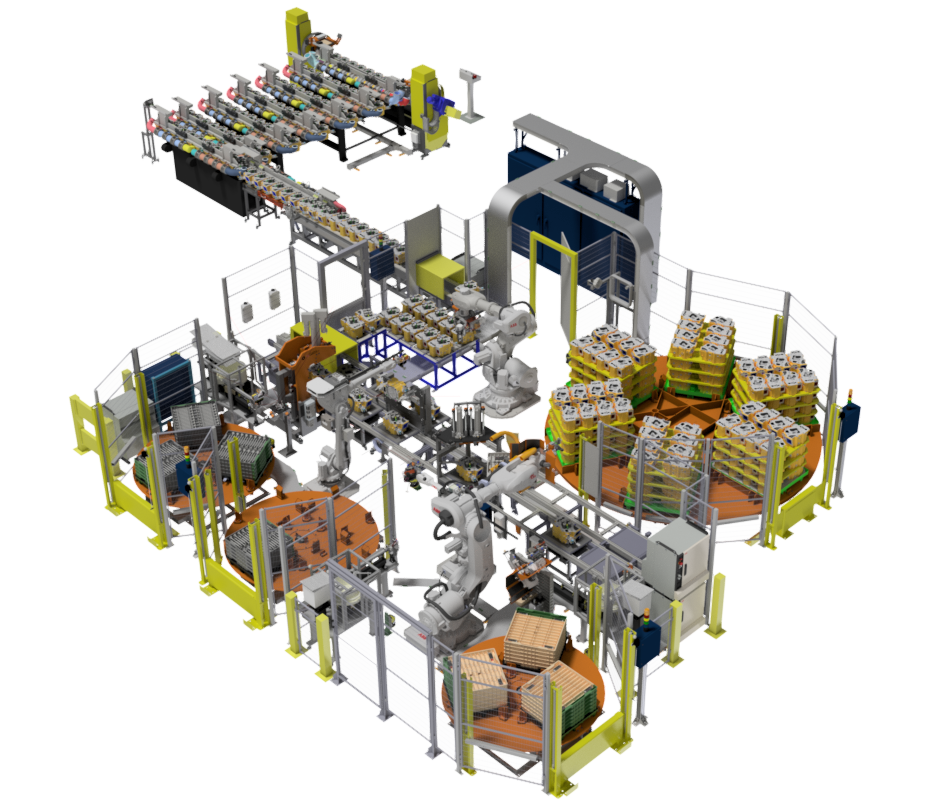