Robotic Paint Stripping
Robotic Blast Booths
rpGatta upgraded four existing manual blast booths to become automatic. We utilized Fanuc M710iC robots mounted overhead on a Gudel 7th axis linear track. External gantries were custom designed to support the robot and rail on the inside of the booths. All electrical components, including the robot, on the inside of the booths are Class II Division I certified by an NRTL, MET Labs. A camera on the end of arm tooling and three stationary cameras provide live feedback to a control station to allow operation from outside the booth via joysticks. These systems are all set up for pre-programmed and manual operation and capable of operator taught programs. Prior to the installation, the operators were manually blasting the parts wearing full blast suits and respirators. They now sit in the comfort of an air conditioned office where they control and monitor the process via joysticks and remote cameras.
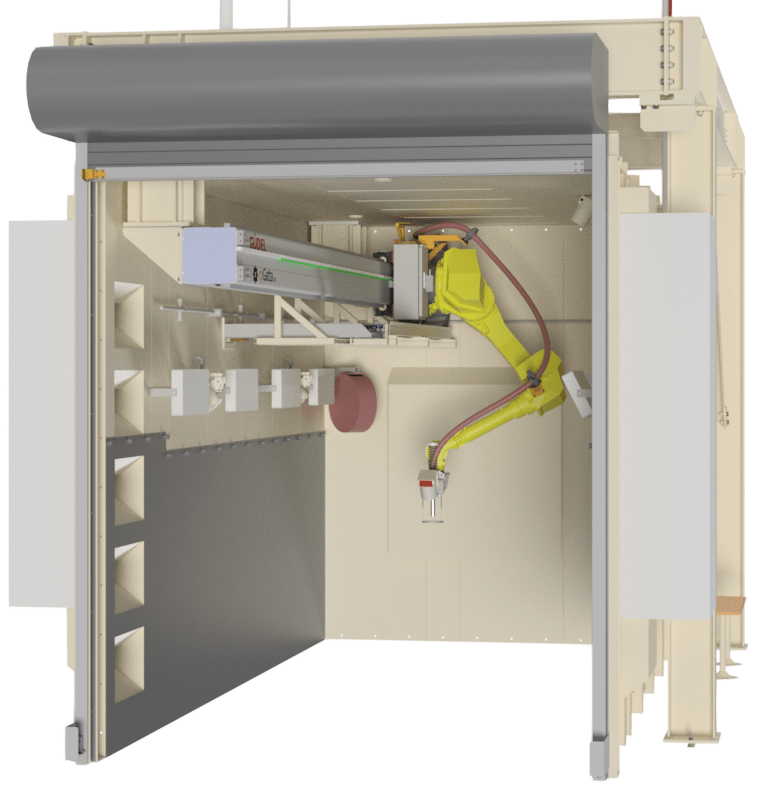
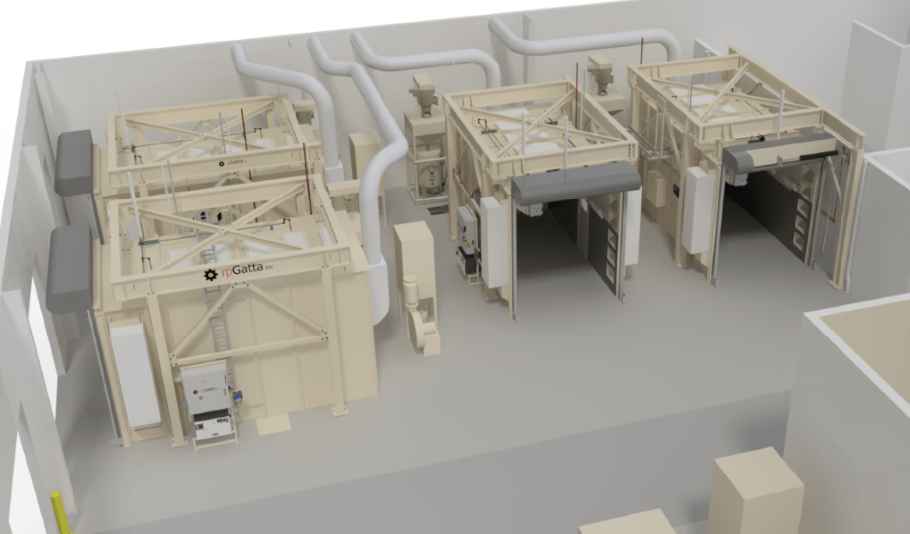
Robotic Chemical Paint Removal System
rpGatta designed and built a C2D1 Robotic Chemical Paint Removal System. This system utilizes 53′ of floor-mounted Gudel rail and 35′ of suspended Gudel rail to mount a Fanuc P350iA/45 robot. The system is driven from the floor-mounted rail on one side and the other side is supported by heavy duty casters so that large airplane components can be wheeled into the cell from the side. Along with a network of safety sensors and features, this system has a chemical distribution system consisting of multiple fluid systems with lines, pumps, valves, and guns. This system has manual joystick drive functionality for the operator to remotely teach paint removal processes with the aid of six explosion-proof IP cameras to view the inside of the cell. We integrated a LIDAR scanner on the carriage to automatically create a 3D point cloud of the parts inside the booth for a quick, easy setup.
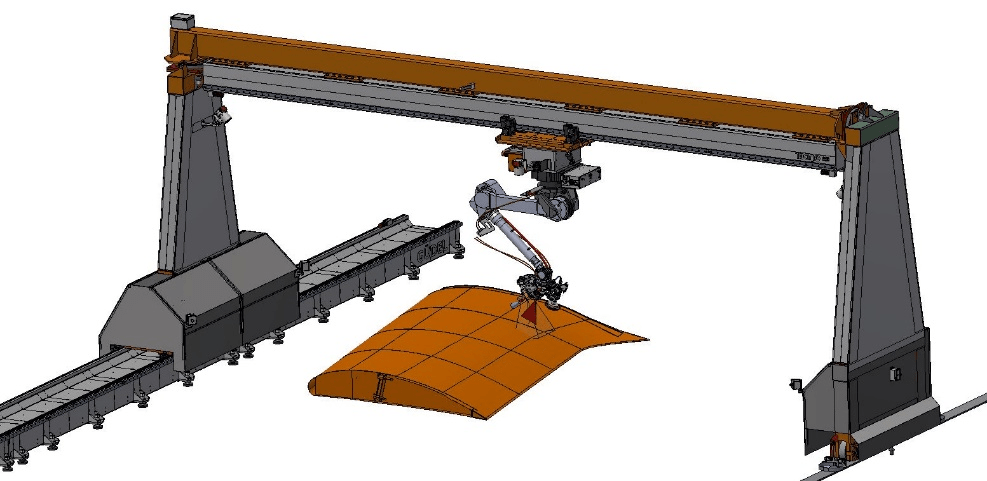

Robotic Grit Blast System
rpGatta designed and built a custom Robotic Grit Blast Booth System. This system utilizes a Fanuc P350iA/45 robot mounted to a bridge rail that’s mounted on two runway rails to add two additional axes to the system to allow for blasting access around the entire component. Along with the robotic system, rpGatta also provided the booth, blasting, and recirculation equipment for the media. Lidar scanners and 3D cameras on the robot’s end of arm tooling allowed the system to create a 3D point cloud of the components inside of the booth. Utilizing rpGatta’s offline path planning software, operators were able to automatically create custom robot paths for the de-painting processes.
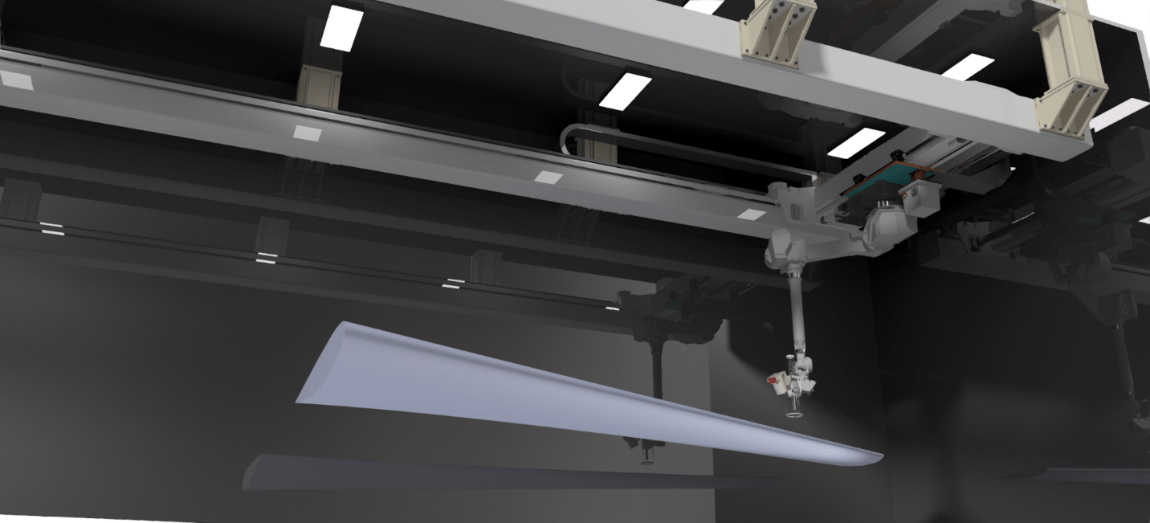
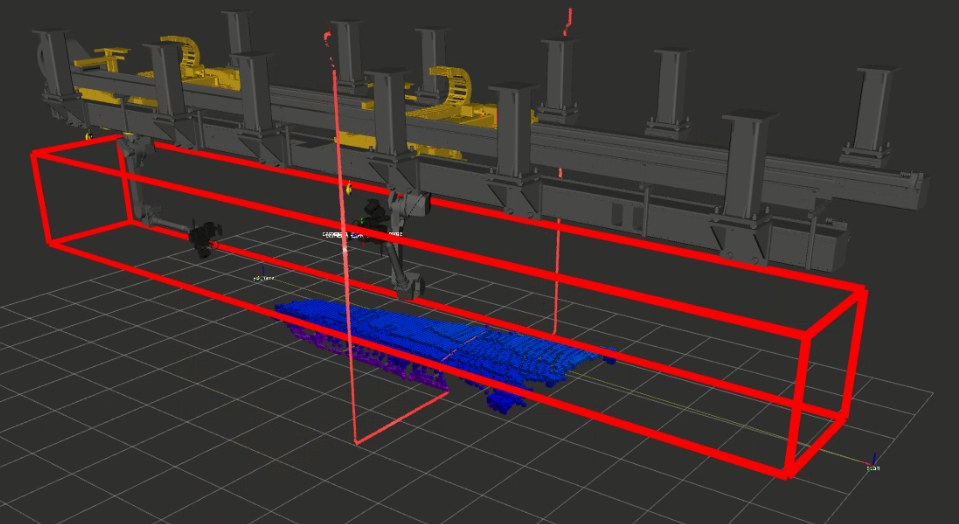
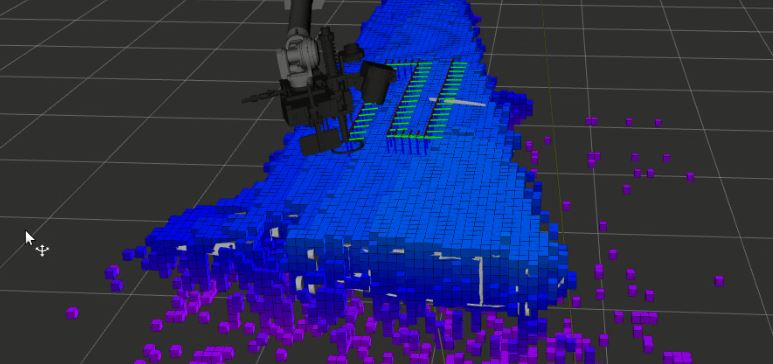
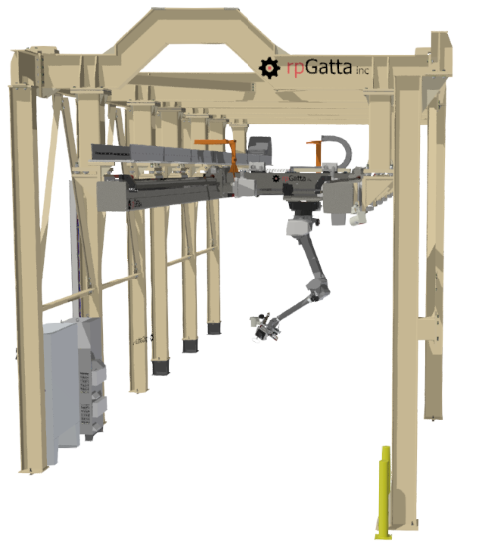
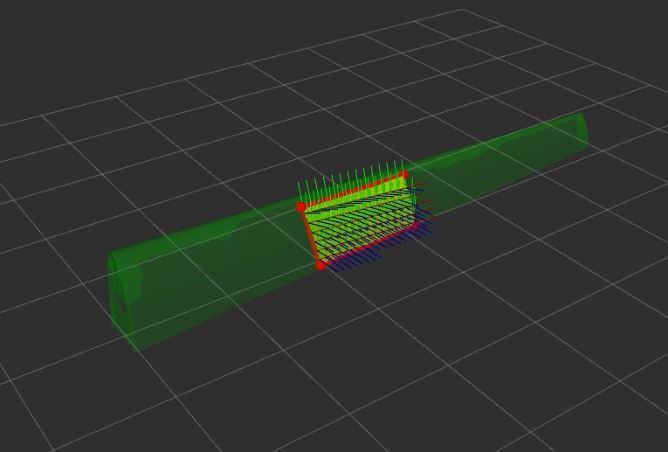
Robotic Sanding Systems
rpGatta designed and built multiple Robotic Sanding Systems. The project scope is similar to the four Robot Blast Booths because the system has an external gantry that was designed around the existing booth to support the robot and rail on the inside, and it has a manual control station with joysticks for remote operation. The sanding end effector is compliant in multiple directions for a smooth, consistent finish.
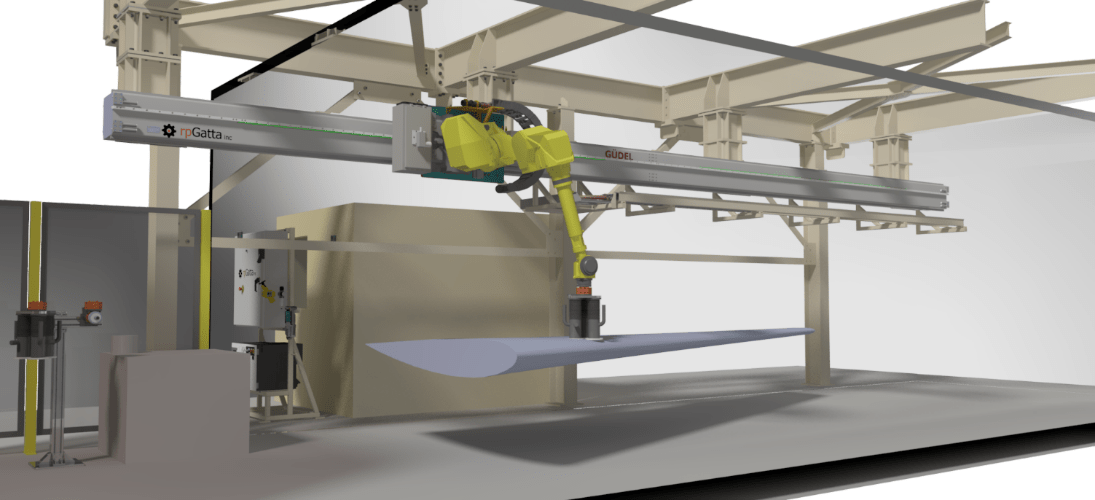

Horizontal Stabilizer Fixtures
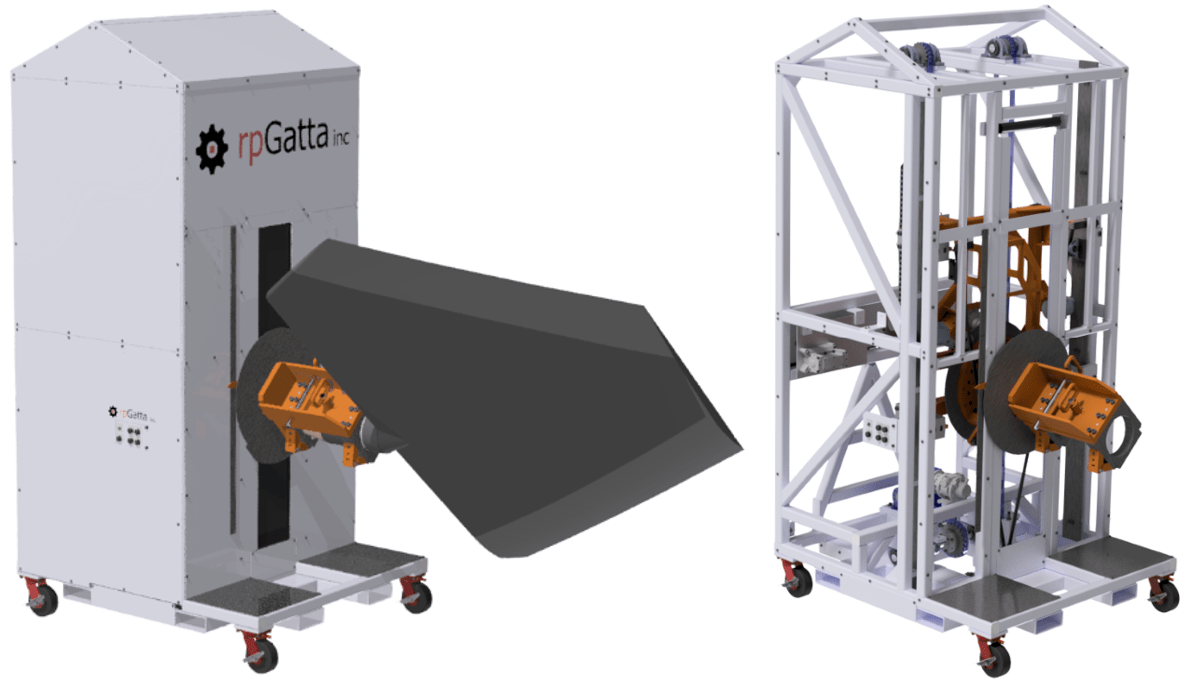
Features:
- rpGatta designed and built (8) portable fixtures
- Each fixture clamps the shaft of an aircraft horizontal stabilizer
- The operator presses buttons to lift and rotate the stabilizer to assist in the manual paint stripping and applying processes
- These fixtures are explosion-proof and rated for a Class II Division I environment
- The systems utilize pneumatic spring applied caliper disk brakes that disengage when the buttons are held and automatically brake when the buttons are released
- There are pneumatic limit switches strategically positioned such that when the moving clamp mechanism contacts them the brakes will instantly engage to prevent the stabilizer from ever contacting the ground