Assembly Machines
Clutch Fan Housing Assembly Cell
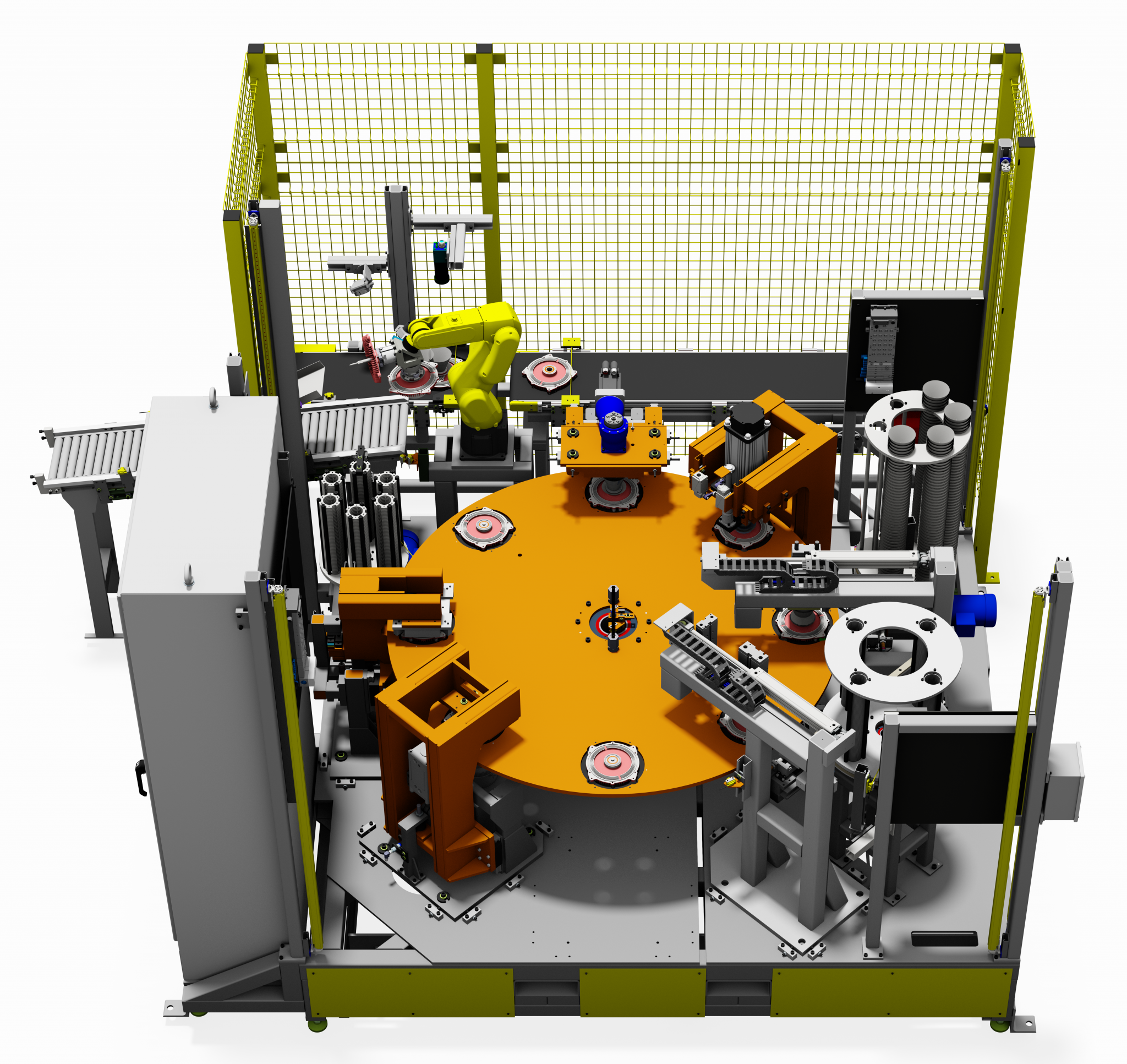
Features:
- 8 Station Cam Actuated Dial Table
- 6-Axis Robot with Triple Grippers
- Base Frame to mount the robot and all stations
- In-feed and Out-feed conveyor
- Reject Gravity Fed Accumulation Conveyor
- Machined Body Orientation Station
- Pick-Up Ring Dispensing Station
- Load/Unload Station
- Pressure Testing Station
- Pick-up ring riveting station
- Bearing & Body Identification/Bearing Place Station
- Bearing Boss Ring Place Station
- Bearing & Bearing Boss Ring Press Station
- Bearing Stake/Lip Roll Station
- Free Standing Controls Enclosure
- Safety Guarding with Interlocked Access Doors
Corner Module Assembly Station
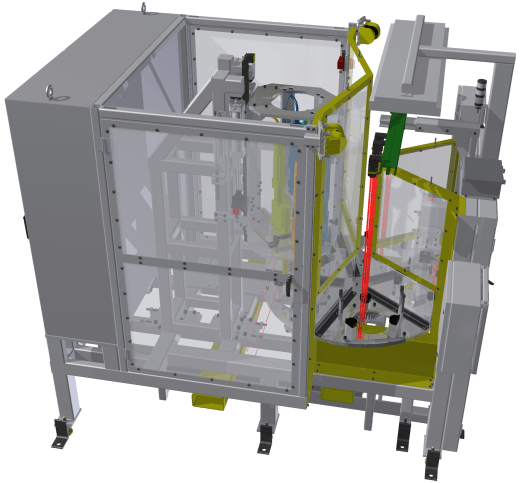
Features:
- The Corner Module Assembly Machine semi automatically assembles the manually loaded parts in (5) stations situated around a dial table
- The machine can has part detection and error proofing in every station to ensure proper assembly sequence of right hand and left hand corner module parts:
- rotor
- bearing hub
- dust cover guard
- knuckle
- calipers
- 6 fasteners
- The machine has an integrated (6) spindle torque tool multiple that stores the torque data via the plant network quality system against a part number assigned via a highly reliable 2D barcode reader camera & light system
- The rotor and hub are run out with reliable laser readings accurate within 1 micron [~0.0002″]
- The machine can be run in one or two operator mode via two operators stations each with their own operator adjustable HMI screens
- A third large touch screen diagnostics HMI with and three (3) safety interlocked access doors and (2) PLSs allow for easy machine maintenance in each station
Steering Knuckle Assembly System
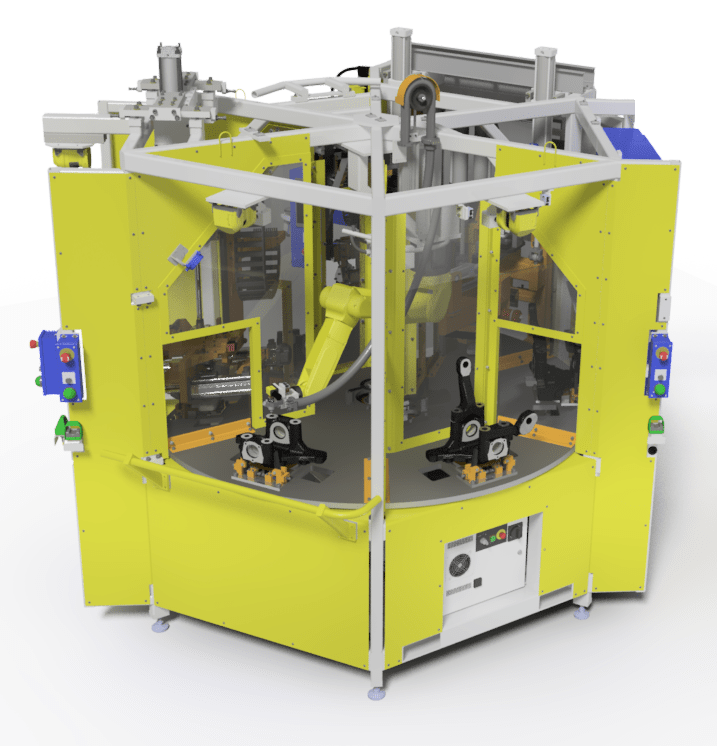
Features:
- Six Station Dial Table
- Handles three different knuckle models and 36 different possible knuckle combinations with the different steer rod and tie rod arms
- Driven by a pinion on a VFD controlled gear motor
Stations:
- Station 1: Load/Unload Steering Knuckles & Shim Measurement
- Station 2: Servo Bearing Press
- Station 3: Robotic Loctite Apply
- Station 4: Steer Arm, Tie Rod Arm, Bolt Installation
- Station 5: Robotic Vision Verification
- Station 6: Twin Spindle Torque Process
Turbo Clocking Machine
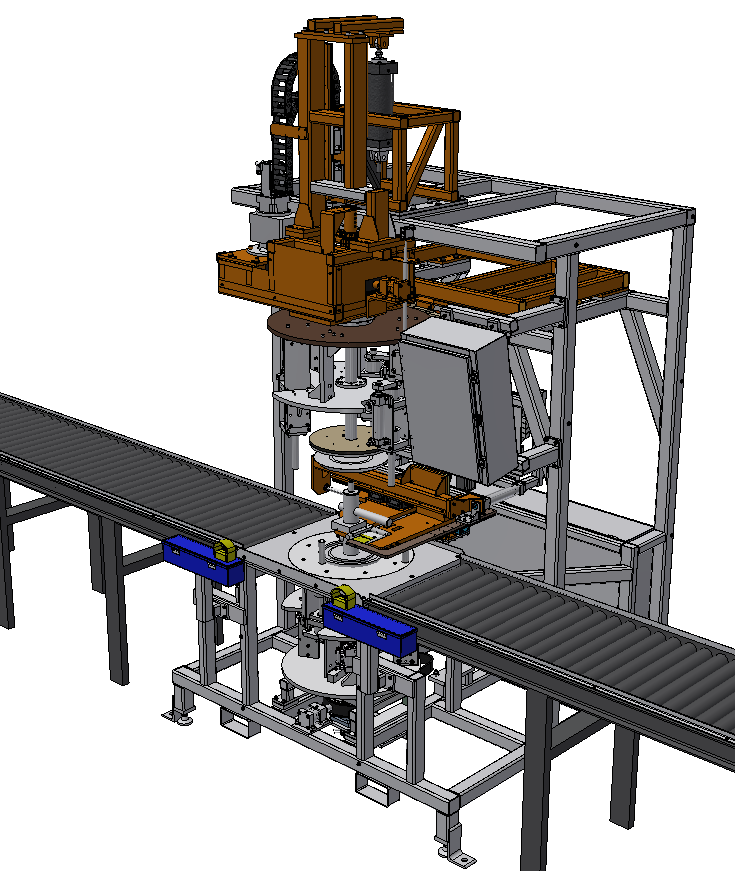
Features:
- Self-contained floor mounting system
- 3-jaw gripper mounted on a pneumatically actuated feed slide grips the outer diameter of the housing
- A stepper motor driven turntable bearing with encoder rotates the housing to the correct angle
- Mechanical stop plates automatically retract back out of the way and allow the operator access to tighten the upper and lower band clamps
- After the band clamps are tightened, the operator will depress the Opto-Touch buttons and the assembly will rotate a preset number of degrees to allow the operator access to the oil drain holes to install fittings
Hub Sub Assembly System
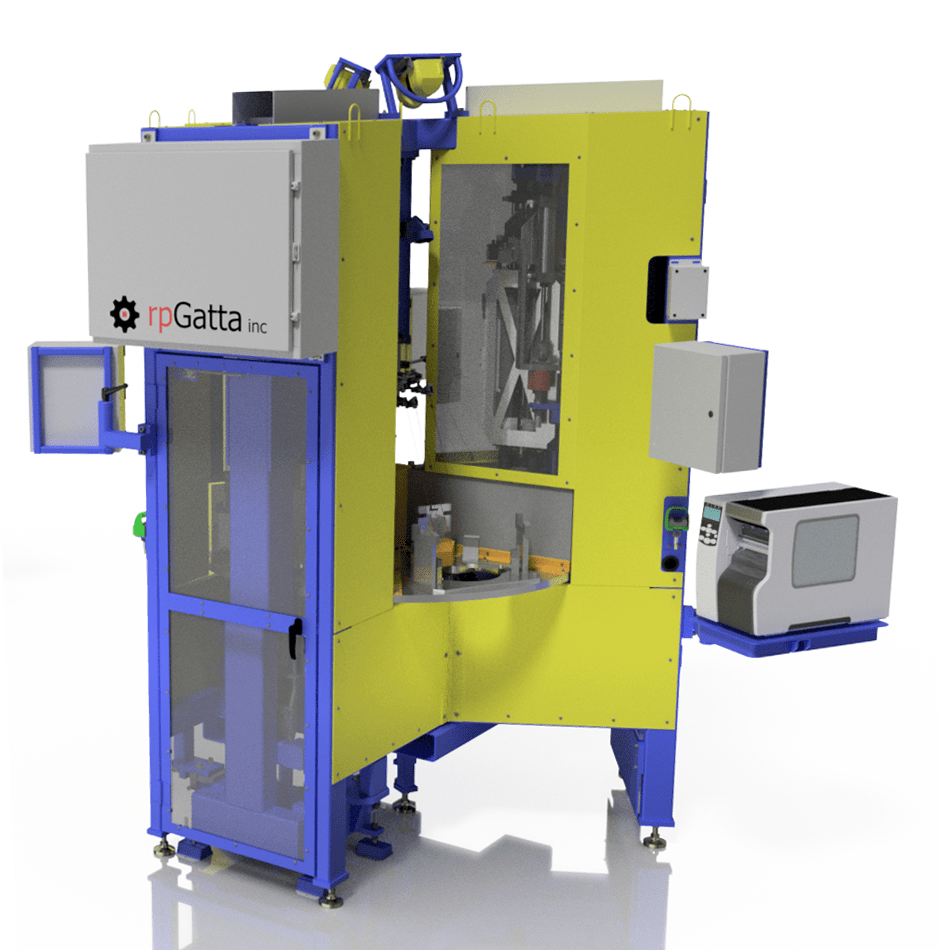
Features:
Electrically Driven Six Station Dial Table
Stations:
- Station 1: Unload/Load New Rotor and Bearing
- Station 2: Rotor Runout
- Station 3: Load Heat Shield, Load Knuckle, Knuckle Bolt Insertion
- Station 4: 4-Spindle Torque Process
- Station 5: Load Caliper, Caliper Bolt Insertion
- Station 6: 2-Spindle Torque Process
- Standalone Dually Fastening System
Steering Knuckle Assembly System
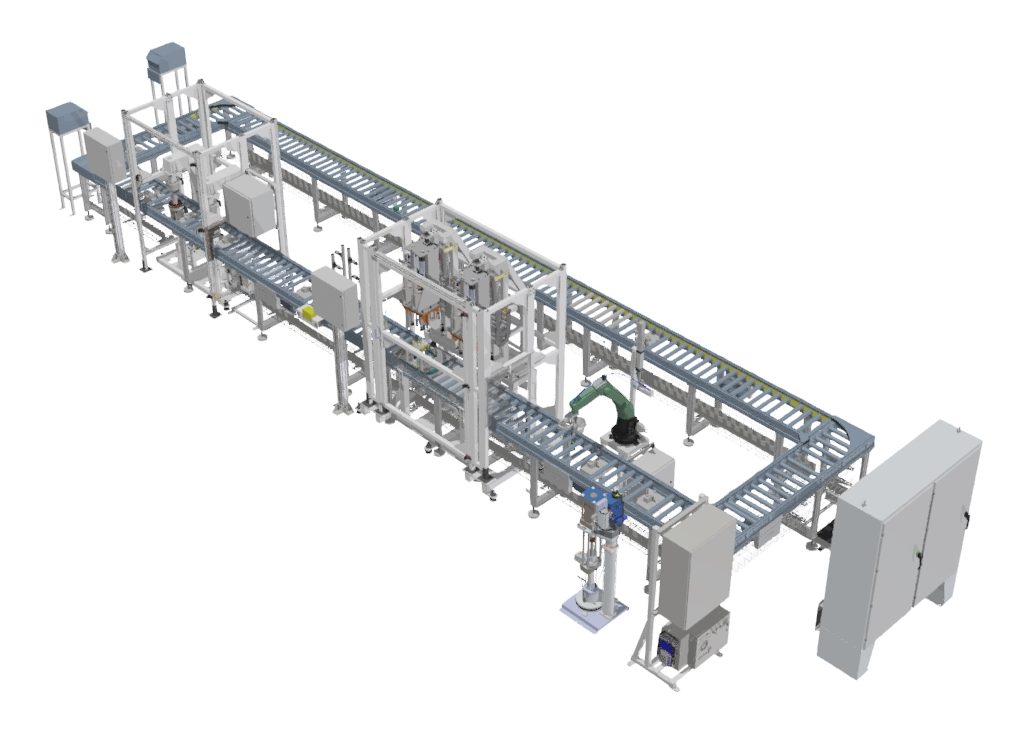
Features:
- This loop conveyor assembles automotive car knuckle assemblies
- Station 1: Operator unloads the finished assemblies and installs them to the frame on the line then loads new knuckle bodies, rotors, and bearing hubs onto RH and LH pallets
- Vision confirms that the knuckles were loaded properly
- Barcode reader scans the printed out barcode associated with each knuckle
- Station 2: Automatic rotor runout for both RH and LH knuckles
- Station 3: Operator loads dust shield and calipers onto the knuckle assembly and hand starts the bolts
- Station 4: Vision and lasers error-proof the correct parts were loaded onto the assemblies
- Station 5: Dual multi-spindle assemblies lower onto the RH and LH assemblies to simultaneously torque six bolts at a time
- Station 6: Collaborative robot applies a ring of grease to the hub bearing and uses vision to error-proof the dispensing bead
- Station 7: Buffer for 16 completed RH and LH assemblies
- Station 1: Operator unloads the finished assemblies and installs them to the frame on the line then loads new knuckle bodies, rotors, and bearing hubs onto RH and LH pallets
Track Press Fixture
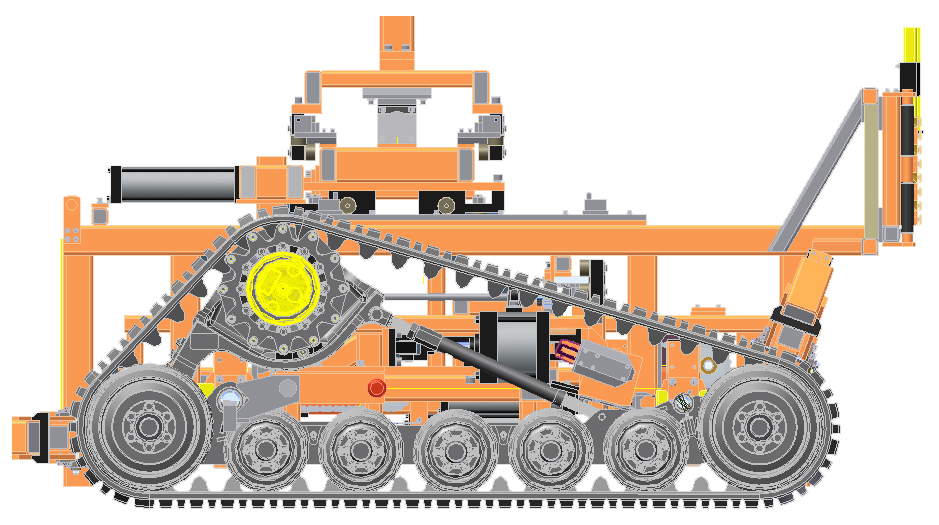
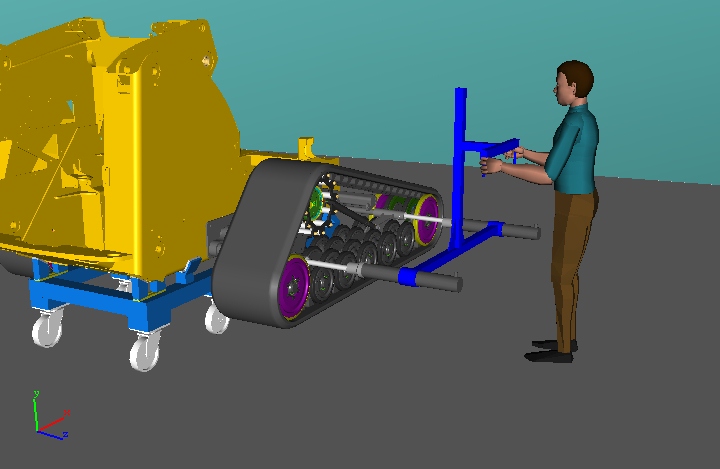
Features:
- This operator-controlled assist picks and loads the RH and LH tracks onto steer skid loaders
Cylinder Head Assembly Line
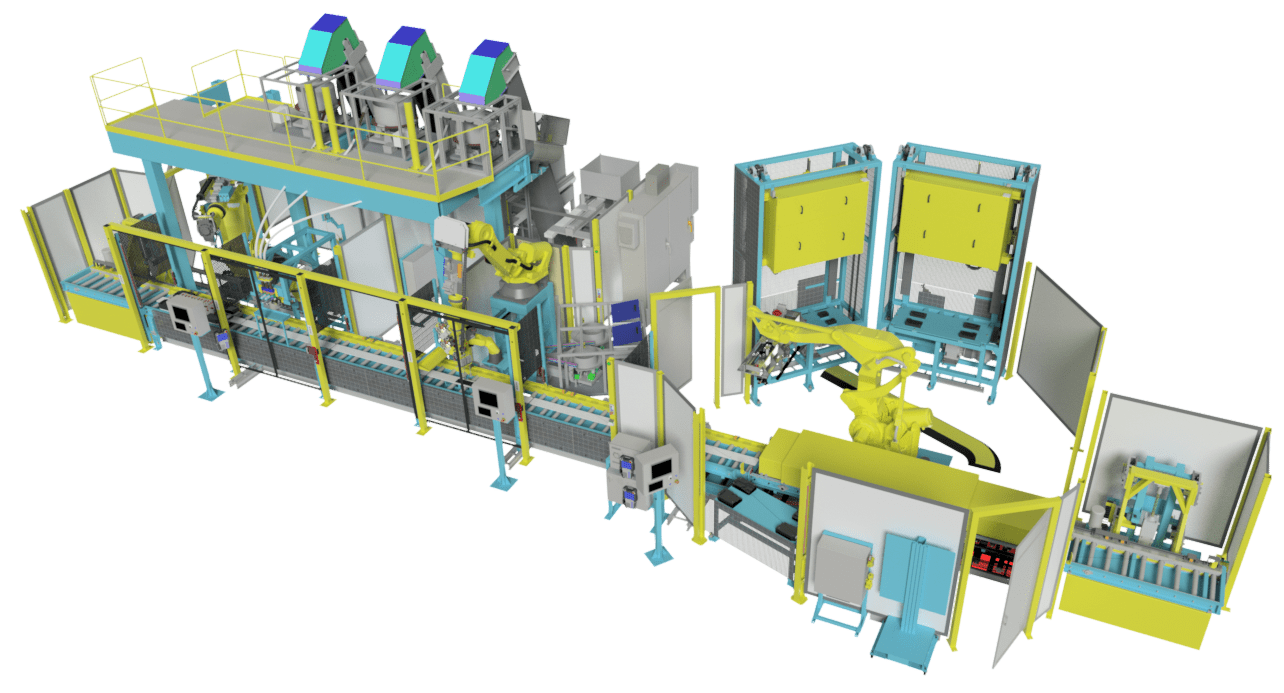
Features:
- 63 feet long recirculating pallet conveyor with elevators on each end
- Utilizes a total of five Fanuc robots
- Multiple manual and automated assembly stations
- Accommodates three different models of engine cylinder heads with the flexibility to accommodate additional future models
- Utilizes three bowl feeders for orienting and accumulating different size springs for each model
- Utilizes two bowl feeders for orienting and accumulating small keepers
- Utilizes two custom cam-designed cylinder head spring exercisers for testing and quality assurance